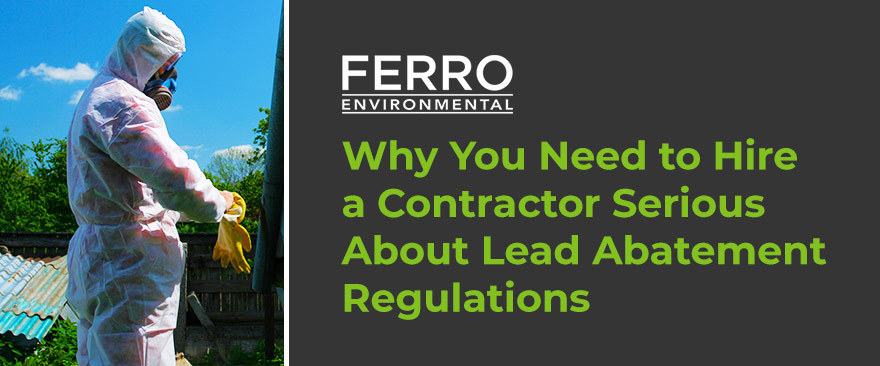
Lead Abatement Regulations
Lead is widely used for industrial and commercial purposes, mostly because it is available and useful for producing common items such as traffic signs. But lead is also hazardous. When inhaled, the substance can easily travel to soft tissues ( liver, kidneys, lungs, muscles, heart, and brain) and severely harm us in many ways – such as causing nerve damage. Worse, symptoms of lead exposure can take years to emerge after chronic long-term exposure.
It’s crucial that residences, schools, workplaces and other areas where people spend most of their time are free of lead contamination. Since the 1970s, significant work has been done in removing lead from buildings. But there is still significant room for improvement; as recently as October 2017 the Ontario government found that 640 schools in the province failed in limiting lead exposure to students and faculty.
Lead abatement is not a trivial task. Rather, lead abatement is a thorough process defined by strict federal and provincial laws and regulations. Lead abatement regulations aim to guarantee that the lead removal process in your home, workplace or school is done in a safe and effective manner, ensuring the health and safety of both workers and occupants.
Know What to Expect from Your Lead Abatement Contractor
In Ontario, lead abatement regulations are defined under the Occupational Health and Safety Act (OHSA). Under Section 6 of the OHSA, lead abatement operations can be placed under one of three categories: Type 1, Type 2 and Type 3. In addition, all lead abatement operations need to fulfill specific requirements in terms of area management and worker preparation.
These minimum requirements include accessibility to washing facilities comprising of a wash basin, water, soap and towels for workers, who must use these facilities before eating, drinking, smoking and/or leaving the work area. In addition, workers are prohibited from eating, drinking, smoking or even chewing gum in the work area. The contractor is also required to place drop sheets at the work area to catch dust, chips and other debris.
Besides preparing the work area, the contractor is also required to undertake a proper cleaning and waste management process. This includes using a High Efficiency Particulate Air (HEPA) filter-equipped vacuum to clean the work area at regular intervals. The waste must be placed in a dust-tight container which is clearly labelled for containing lead waste. The contractor must also regularly replace the container throughout the lead abatement process.
In addition to the basic requirements, the lead abatement regulations in the OHSA also set out specific requirements based on the kind of lead abatement project you are taking on:
- Type 1 Operations: The basic requirements above should be sufficient, but if a worker requests it, then the employer must provide a breathing mask (i.e. half-mask particulate respirator with N, R or P-series filter with 95%, 99% or 100% efficiency.
- Type 2 Operations: All Type 02 lead abatement operations require fully visible signs to clearly state that the work area has lead dust, fume and/or mist hazards. Respirators are mandatory for all those in the work area, which itself must be restricted to authorized persons with protective clothing.
- Type 3 Operations: The work area must be partially or fully enclosed such that no lead contamination, such as dust, reaches non-work areas. These enclosures must be made of windproof materials and use secure structures. Lead paint abatement contractors with indoor work areas and/or dealing with lead paint (i.e. Type 3b) must use full enclosures (no exposure). In addition, barriers should be there to prevent unauthorized access to the work area, itself off-limits to those without adequate protective clothing.
Type 3b work areas must also include a nearby decontamination facility in which workers can change into and from protective clothing. This must also include a shower with a hot and cold water temperature range of exactly 40-50°C as well as a HEPA-filter vacuum. Workers must also follow OHSA-set procedures at the decontamination site.
Each province has its own lead abatement regulations, such as the Occupational Health and Safety Code in Alberta, the Environmental Management Act in British Columbia and others, but overall, it is important to comply with your area’s worker safety, waste management, and hazard policies. For example, Ferro Canada is a member of the Environmental Abatement Council of Ontario, which requires strict compliance with the OHSA.
Next Steps
To safely and successfully to remove lead, you must get in touch with an experienced contractor that properly abides by lead abatement regulations. Doing so will guarantee that your project will keep the health and safety of the lead removal workers and your occupants or neighbours top of mind. Contact us if you are preparing for a lead abatement project, Ferro Canada will conduct a detailed assessment and safely and permanently remove this hazardous substance.